Last Updated on July 14, 2025 by Jaxon Mike
Servo motors are a type of actuator widely used for precise position control applications like robotics, CNC machines, and RC vehicles. Unlike standard DC motors, servo motors have built-in control circuitry that allows them to rotate to and hold at a specific angular position.
There are several different types of servo motors, with two of the most common being coreless servo motors and brushless servo motors. Both types provide precise, controlled motion but have important differences in their design and performance.
In this article, we will compare coreless vs brushless servo motors, looking at how each one works, their pros and cons, and typical applications where they are used. Understanding the differences between these two servo types will help you select the right option for your needs.
Comparison Table
Features | Coreless Servo Motors | Brushless Servo Motors |
Construction | – Slotless stator with ironless windings [Cylindrical permanent magnet rotor] No brushes or commutator | – Slotted stator with multiple windings [Rotor has surface mounted magnets] Electronic commutator |
Torque | Lower torque capacity due to weak permanent magnets | Higher torque capacity from stronger electromagnets in the stator |
Speed | Typically lower max RPM speed | Higher max speed capabilities |
Efficiency | Lower efficiency results in more heat generation | More efficient use of electrical energy with less waste heat |
Noise | Very quiet operation with no cogging or brush noise | Audible noise from cogging torque and switching |
Response Time | Very fast response for position changes | Slightly slower response due to rotor inertia |
Accuracy | Good accuracy but may be lower at high speeds | Very high accuracy and position precision |
Lifespan | Shorter lifespan due to weak rotor magnets | The brushless design has a long working life |
Complexity | Simple and low-cost construction | More complex electronics are required for control |
Maintenance | Minimal maintenance required | Electronic controls may need calibration |
Use Cases | Hobby servos, small robots, RC vehicles | Industrial automation, CNC machines, aerospace |
Price | Check Latest Price | Check Latest Price |
How Servo Motors Work
All servo motors consist of three basic components:
- Motor – Provides the rotational force or torque. This is usually a permanent magnet DC motor.
- Potentiometer – Measures the current angular position of the motor’s output shaft.
- Control circuitry – Compares the potentiometer feedback to the desired position and controls power sent to the motor to reach and maintain the correct angle.
This closed feedback loop allows a servo motor to rotate its output shaft to a specific angular position and hold it there until a new position is commanded. The control circuitry will continuously adjust power to the motor as needed to compensate for any load disturbances to maintain the desired angle.
Now let’s look at the specific differences between coreless and brushless servo motors.
Differences Between Coreless and Brushless Servo Motors
Coreless and brushless servo motors differ significantly in their construction and performance characteristics:
Construction and Design
- Rotor – The coreless motor has a cylindrical permanent magnet rotor while the brushless motor has a rotor with magnets mounted on its surface.
- Stator – The coreless motor stator is a slotless ironless winding while the brushless motor has a slotted stator with multiple windings.
- Commutator and Brushes – The coreless motor does not have a commutator or brushes while the brushless motor uses an electronic commutator controlled by the drive electronics.
Performance
- Torque – Brushless motors generally have higher torque capacity than coreless motors.
- Speed – Maximum speeds are higher on brushless servo motors.
- Efficiency – Brushless motors are more efficient with less electrical energy converted to heat.
- Noise – Coreless motors operate very quietly with no brush or cogging noise.
- Lifespan – Brushless motors last longer since they have no brushes to wear out over time.
Use Cases
- Hobby Servos – Coreless motors are very common in low-cost hobby servo due to their simplicity and low noise.
- Industrial Automation – Brushless motors are widely used in factory automation for their higher power density and accuracy.
In summary, while both types of servo motors use closed-loop feedback for precise control, brushless servo motors tend to provide better torque, speed, efficiency and lifespan while coreless servos offer quiet operation in a compact package.
Pros and Cons of Each Type
To further understand the trade-offs, let’s look at the key benefits and downsides of each servo motor technology:
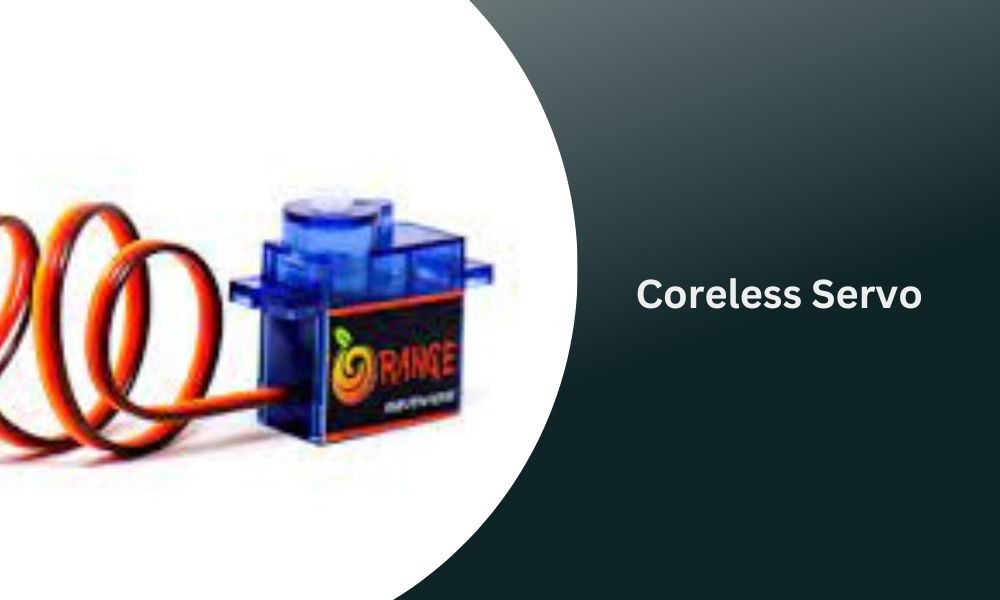
Coreless Servo Motors
Pros:
- Very compact and lightweight design
- Operate very quietly
- Simple construction with few components
- Low inertia for quick acceleration/deceleration
- No cogging torque ripple
Cons:
- Low torque capacity
- Generate more heat at higher loads
- Low maximum RPM speed
- Prone to overheating damage
- Shorter lifespan due to weak magnets
Brushless Servo Motors
Pros:
- Provide very high torque in a small package
- Efficient and run cooler than coreless motors
- Higher max speeds possible
- No brushes to wear out over time
- Typically more accurate and less noise
Cons:
- More complex construction
- Require electronic speed control
- Cogging torque can cause vibrations
- Operation produces some audible noise
- Generally more expensive than coreless
In summary, coreless servo motors excel in applications where low noise, rapid response, and simplicity are critical, such as radio-controlled models and small robotics projects.
Brushless servo motors are the choice where high torque, efficiency, accuracy and reliability are needed, such as CNC machines, factory automation, aerospace, and advanced robotics applications.
FAQs
What is the main difference between a coreless and brushless servo motor?
The key difference is that a coreless servo motor has a simple slotless stator and permanent magnet rotor while a brushless servo motor uses a slotted stator with multiple windings and an electronic commutator instead of brushes.
Which type of servo motor has higher torque?
Brushless servo motors generally can produce higher torque for their size compared to coreless servo motors. The more complex stator windings allow brushless motors to generate greater magnetic force.
Are coreless servo motors maintenance free?
Yes, one advantage of coreless servos is they do not have brushes that wear out over time, so they require very little maintenance other than occasional lubrication of bearings. They also don’t need any electronic speed controls.
What are some common uses for coreless servo motors?
Coreless servos are widely used in radio-controlled vehicles/planes, small robotics projects, laser steering mirrors, and other applications where low speed, quiet operation and rapid response is critical.
Why are brushless servos better suited for industrial automation?
Brushless servo motors are popular in factory automation for their higher power density, efficiency, accuracy and longer working life. Their electronic control also allows for more precise speed/torque regulation.
Conclusion
Coreless and brushless servo motors use closed-loop feedback for precision angular position control. Key differences in their design and performance make each technology better suited for certain applications.
Coreless servos are known for their quiet operation and fast response times but have limited torque capacity and short lifespans. Brushless servos provide higher power, speed and efficiency but at higher cost and complexity.
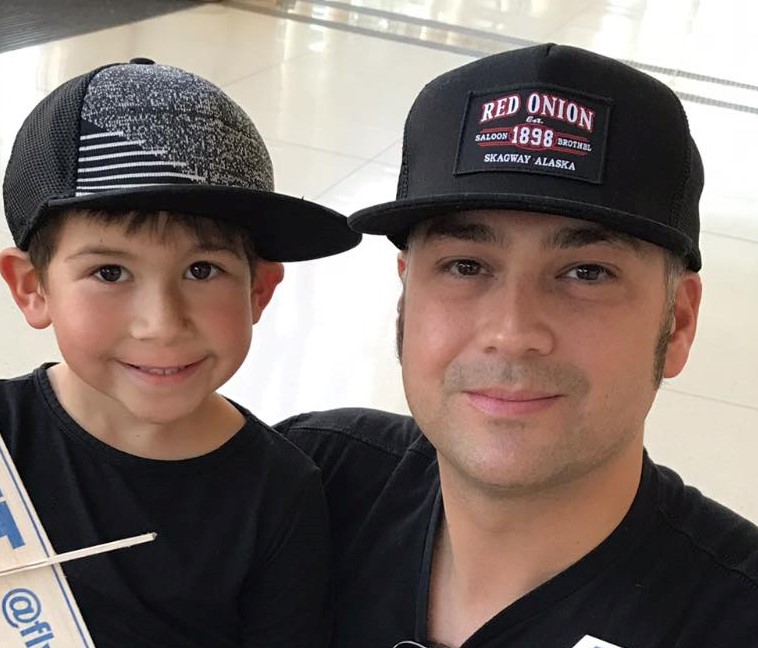
I am Jaxon Mike, the owner of the Rcfact website. Jaxon Mike is the father of only one child. My son Smith and me we are both RC lovers. In this blog, I will share tips on all things RC including our activities, and also share with you reviews of RC toys that I have used.