Last Updated on December 8, 2023 by Jaxon Mike
Gears and pinions are both essential components in mechanical power transmission systems. Though they look quite similar, there are some key differences between gears and pinions that affect how they function and their applications.
In this article, we’ll provide an overview of gears and pinions, explain the differences between them, discuss when to use each, and provide some considerations for selecting and maintaining these important mechanical elements.
Gaining a solid understanding of gears vs. pinions will help engineers, designers, and maintenance professionals choose the right component for their specific needs.
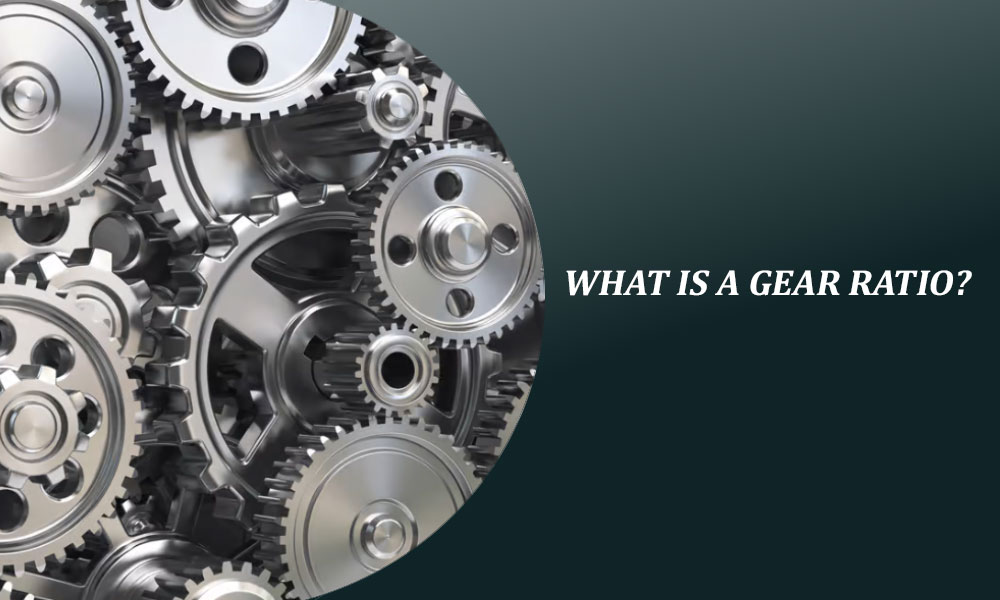
comparison table for gears vs pinions:
Gear | Pinion | |
Definition | Toothed wheel that meshes with another to transmit motion | Smaller driving gear that meshes with a larger gear |
Size | Typically larger than the pinion it meshes with | Always smaller than the gear it drives |
Orientation | Driven component | Driving component |
Rotation | Rotates more slowly with higher torque | Rotates more quickly with lower torque |
Direction | Rotates opposite of pinion | Rotates opposite of gear it drives |
Teeth | Generally has more teeth than pinion | Has fewer teeth to achieve speed reduction |
Common Types | Spur, helical, bevel, worm | Spur, helical, bevel, worm |
Applications | Broadly used to change speed, torque, direction | Often used as input drive in gearboxes, speed reducers |
Materials | Steel, aluminum, brass, plastic | Steel, aluminum, cast iron, powdered metal |
Manufacturing | Machining, hobbing, molding | Machining, hobbing, powder metal sintering |
Cost | Lower due to the smaller size | Broad utility handles higher loads |
Advantages | Broad utility, handles higher loads | Compact, fits in tight spaces, lower inertia |
Disadvantages | Larger space required | Lower torque capacity, driveshaft loads |
What is a Gear?
A gear is a toothed wheel that meshes with another toothed part to transmit rotation and torque. The teeth on mating gears interlock so that when one gear rotates, it drives the adjoining gear to rotate as well.
Gears are used in many applications to:
- Increase or decrease speed (through gear ratios)
- Increase or decrease torque
- Change the direction of rotation
- Move rotational motion to a different axis
Some common types of gears include:
- Spur gears – Cylindrical gears with teeth parallel to the axis of rotation. These are the simplest and most common types of gear.
- Helical gears – Cylindrical gears with angled teeth that are slanted relative to the axis. This makes them run more smoothly and quietly.
- Bevel gears – Conical-shaped gears where the teeth are cut at an angle. This transmits rotation between perpendicular intersecting shafts.
- Worm gears – Used to transmit high reductions between non-intersecting shafts. A worm (screw) meshes with the worm gear (toothed wheel).
- Rack and pinion – A linear gear (rack) that meshes with a rotary gear (pinion) to
- convert between rotational and linear motion.
Gears are commonly used in motors, pumps, transmissions, conveyors, watches, and many other mechanical systems. The advantages of gears include:
- Smooth running and quiet operation (especially helical gears)
- Capability for high-speed operation
- Reversible direction of rotation
- Compact size compared to other speed-changing options
- Ability to go around corners or obstacles using bevel gears
What is a Pinion?
A pinion is a gear, specifically one that is smaller than the gear that it drives. In most applications, the larger driven gear is called the gear, while the smaller driving gear is called the pinion.
Pinions, like gears, have teeth cut into their circumference that interlock with the teeth on a mating gear. When the pinion rotates, it transmits torque to turn the driven gear.
Common types of pinions include:
- Spur pinions – Cylindrical with straight teeth parallel to the rotational axis.
- Helical pinions – Angled teeth slanted relative to the axis for smoother, quieter operation.
- Bevel pinions – Conically shaped to mesh at an angle between perpendicular shafts.
- Worm pinions – The worm gear driven by a worm in a non-intersecting setup.
Pinions are widely used as the driving component in gear sets for speed and torque modification, including applications like:
- Gearboxes
- Speed reducers
- Transmissions
- Differentials
- Rack and pinion mechanisms
The compact size of pinions makes them advantageous, allowing:
- Space savings in tight designs
- Lower inertia for responsiveness
- Ability to drive much larger mating gears
Gear vs Pinion – Key Differences
While gears and pinions appear quite similar, there are some important differences between these two components:
Teeth and Orientation
- Gears usually have more teeth than pinions they mesh with. The gear is driven, while the pinion provides the driving force.
- Orientation is different – a gear is driven, while a pinion drives the mating gear.
Meshing and Rotation
- When meshing, the pinion rotates faster than the gear. The gear has a larger diameter so its linear tooth speed is faster, though rpm is slower.
- The rotation direction is opposite between meshing gears and pinions. The pinion drives the gear in the opposite direction.
Size and Applications
- Pinions are always smaller than the gear they drive for proper meshing. The small size allows pinions to be used in compact spaces.
- Gears are used in a broader range of applications than pinions. Pinions are more often used as the driving component in a gear set.
Materials and Construction
- Gears are commonly made of steel, while pinions may use steel or lighter materials like aluminum or plastic in some cases.
- Gears often have broader faces than pinions to distribute loads. Pinions can have narrower faces since they see lower forces.
When to Use?
Speed Reduction
Pinions are often used as the driving gear in speed-reducer applications. The small pinion with fewer teeth drives a larger gear to achieve a gear reduction. This multiplies torque while reducing speed.
Torque Multiplication
The opposite setup, with a large low-speed gear driving a small pinion, can multiply torque. This is common in differentials – a large ring gear turns slower but with higher torque to drive the pinion.
Direction Change
Meshing gears and pinions rotate in opposite directions. Orienting them on perpendicular shafts creates a direction change in power flow. Bevel gears and pinions are designed for this.
Applications
- Transmissions use various combinations of gears and pinions to shift speeds and torque capacity.
- Gearboxes reduce the speed between a motor and output using different-sized meshing gears/pinions.
- Rack and pinion sets convert rotational motion to linear. A pinion often drives a linear rack gear.
- Worm gear sets use a worm pinion to drive worm gear for high reductions.
- Automotive differentials use a large ring gear driven by the driveshaft to turn a smaller pinion gear.
Gear and Pinion Selection Considerations
There are several important factors to keep in mind when selecting gears and pinions for an application:
Size and Ratios
- Choose appropriate diameters for the speed ratio needed. Large gear diameters coupled with small pinion diameters provide high-speed reductions.
- Gear ratios must match. Pay close attention to the number of teeth on meshing gears/pinions.
Materials
- Hardened steel allows high strength and long wear life for gear teeth. Softer or plastic materials can also work for lower torque applications.
- Consider corrosion resistance depending on the operating environment. Stainless steel gears resist corrosion better than plain carbon steel.
Lubrication Needs
- Enclosed oil bath or grease packing provides the best lubrication. Some applications may require engineered synthetic oils.
- Open gearing requires proper lubricant selection and frequent reapplication.
Noise and Vibration
- Helical, herringbone and other designs can reduce noise and vibration issues common with spur gears.
Proper selection considering these factors will ensure optimal performance and long service life from gear and pinion sets. Next, let’s go over some key maintenance practices.
Gear and Pinion Maintenance
To keep gears and pinions operating smoothly:
Inspection
- Check for damaged, cracked, or missing teeth indicating wear or breakage problems.
- Ensure proper alignment between gears and pinions – misalignment can lead to fast wear.
Lubrication
- Maintain proper oil or grease levels to prevent metal-on-metal contact during operation.
Alignment
- Realign any gears/pinions that become misaligned over time due to loosening or bearing wear.
Replacement
- Replace excessively worn or damaged components. Use the same gear ratios and materials in replacements.
Proper inspection, lubrication, alignment, and timely replacement of worn parts will extend the lifetime of gear and pinion sets.
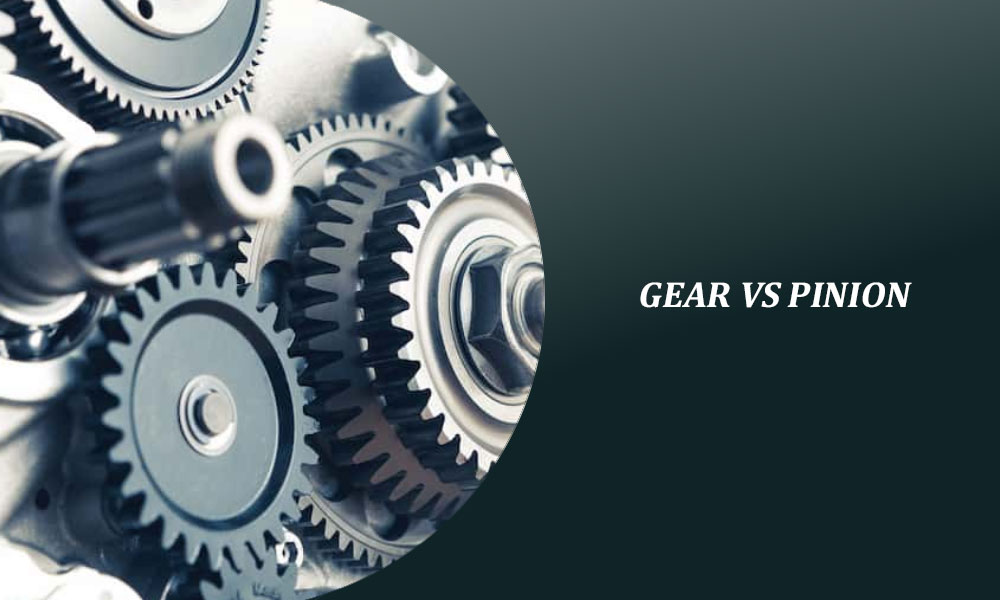
FAQs About Gear vs Pinion
What is the difference between a gear and a pinion?
A pinion is a type of gear that is smaller than the gear it drives. The pinion is the driving component that meshes with a larger driven gear.
When would you use a pinion instead of a gear?
Pinions are often used as the input driving gear in speed reducer and gearbox applications. Their compact size allows fitting them into tight spaces.
What are some examples of pinion applications?
Pinions are used in differentials to drive the ring gear, in rack and pinion mechanisms to drive the rack, and in gearboxes to either increase or decrease speed and torque.
What materials are pinions made from?
Pinions can be made of steel, aluminum, plastic, or other materials depending on the application requirements. Steel provides the greatest strength for high torque needs.
How can you tell if a pinion needs replacement?
Inspect pinion teeth for signs of excessive wear, cracking, or damage. Also check for proper alignment with the gear it drives. Misalignment accelerates wear.
Conclusion
In summary, while gears and pinions serve similar functions in mechanical power transmission, there are some distinct differences that dictate their applications. Understanding these differences allows engineers to select the right components for their specific speed, torque, and direction change needs.
Properly sized, selected, and maintained gear and pinion sets will provide many years of reliable operation.
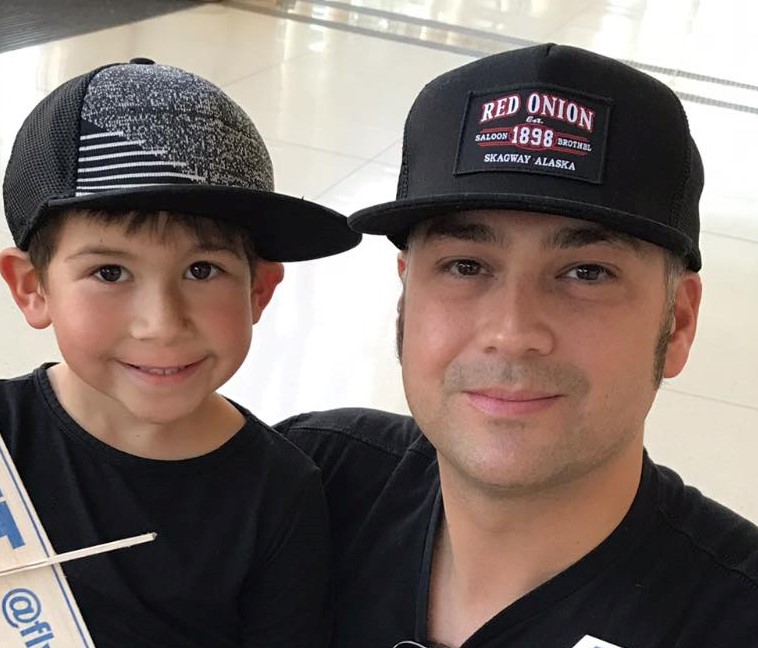
I am Jaxon Mike, the owner of the Rcfact website. Jaxon Mike is the father of only one child. My son Smith and me we are both RC lovers. In this blog, I will share tips on all things RC including our activities, and also share with you reviews of RC toys that I have used.