Last Updated on December 3, 2023 by Jaxon Mike
Brushed DC motors are electric motors that convert electrical energy into mechanical energy through electromagnetic induction. They are powered by direct current (DC) electricity and use brushes and a commutator to deliver power to the rotating armature.
Brushed motors have been around for over a century and continue to be widely used today in everything from small hobby motors to industrial equipment.
In this article, we will look at the basic construction and operation of brushed DC motors, the different types, and the key principles that allow them to generate continuous rotational motion.
What is a Brushed DC Motor?
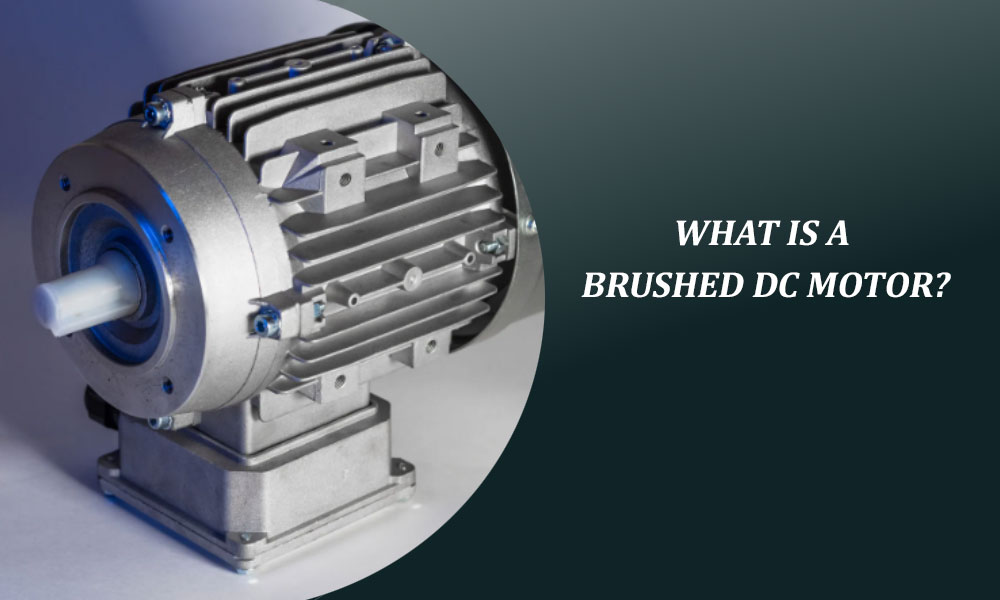
A brushed DC motor consists of two major components – a stator providing a stationary magnetic field and a rotor spinning within that field. The interaction between the permanent magnets of the stator and the electromagnets of the rotor generates rotational motion.
Basic Construction and Components
The main components of a brushed DC motor are:
- Stator – Provides a fixed magnetic field using permanent magnets or electromagnets.
- Rotor (Armature) – Rotates inside the stator and contains the windings that carry current.
- Commutator – A cylindrical assembly mounted on the rotor shaft, divided into multiple metal contact segments. It connects current to the windings.
- Brushes – Conductors, usually made of carbon or graphite, that press against the commutator and deliver current to the rotor windings.
- Axle (Drive shaft) – The output shaft of the motor.
- Housing – Holds all the components together.
- End bells – Covers on each side that enclose the rotor and stator.
How does it work?
In a brushed DC motor, the stator provides a fixed magnetic field while the armature rotates within this field. The commutator and brushes deliver DC current to the windings of the rotor. This generates a magnetic field around the rotor that interacts with the stator’s permanent magnetic field.
According to the principles of electromagnetism, opposite poles attract while like poles repel each other. So the rotor’s magnetic poles are pushed and pulled by the stationary magnetic field, generating rotational motion.
As the rotor turns, the segments of the commutator come in contact with different brushes, causing the current to flow in different directions in the windings. This continually flips the magnetic poles of the rotor, allowing it to keep rotating.
Applications and Uses
Brushed DC motors have some key advantages like simple construction, low cost, high reliability, and easy speed control that make them suitable for a wide range of applications:
- Small fan motors, disk drives, power tools, domestic appliances, toys, actuators, etc.
- Starter motors and windshield wipers in vehicles.
- Industrial machine tools, conveyors, winders, paper mills, textile mills, etc.
- Traction applications like electric bikes, golf carts, electric vehicles, etc.
- Positioning systems in robotics and automation.
Even though brushless DC motors are taking over some applications, brushed motors continue to be extensively used today in many devices and equipment.
Main Types of Brushed DC Motors
There are several different types of brushed DC motors distinguished by how the stationary magnetic field is created:
Permanent Magnet Brushed DC Motors
These contain permanent magnets on the stator to generate the magnetic field. Samarium cobalt and neodymium iron boron are common permanent magnet materials used.
Wound Field Brushed DC Motors
Here the stator consists of field coils that are energized to produce the required magnetic field through electromagnets.
Based on the winding connections, wound field DC motors are further classified into shunt wound, series wound, and compound wound motors.
Series Wound Brushed DC Motors
In series motors, the stator field coils are connected in series with the armature windings. This allows them to draw high starting torque but makes speed control difficult.
Shunt Wound Brushed DC Motors
Shunt motors have stator field coils in parallel or shunt with armature allowing easy speed control. But they cannot provide high starting torque.
Compound Wound Brushed DC Motors
These combine series and shunt windings to get both high starting torque and good speed regulation.
Now that we’ve covered the major types of brushed DC motors, let’s look at the key operating principles that enable them to convert an electrical input to continuous rotational mechanical output.
Operating Principles of Brushed DC Motors
The working of brushed DC motors is governed by three main principles – electromagnetic induction, magnet/current interaction, and commutation.
Electromagnetic Induction
Whenever a conductor moves through a magnetic field, or a magnetic field moves relative to a conductor, it causes electrons in the conductor to move – generating an induced electromotive force (EMF).
In a DC motor, this happens between the stator’s magnetic field and the rotor’s rotating wire windings, inducing an EMF in the rotor coils.
Interaction of Magnets and Current
The induced current flowing in the rotor windings sets up a magnetic field around the rotor. This rotor field then interacts with the fixed stator field as per the laws of magnetism – opposite poles attract and like poles repel.
This push-pull interaction of the two fields applies torque on the rotor, causing it to spin.
Generating Rotational Motion
As the rotor turns, the commutator and brushes switch the direction of current flow in the windings so that the rotor magnetism keeps getting flipped. This allows the rotor to keep rotating in the same direction within the fixed stator field.
So brushed DC motors operate on the principles of electromagnetic induction, magnetism, and commutation to convert electric current into continuous rotational mechanical energy.
Torque Generation in Brushed DC Motors
The torque, or rotating force, generated by a brushed DC motor depends on the strength of the magnetic fields of the stator and rotor.
Factors Affecting Torque
- Number of turns in the armature windings – More turns mean a stronger magnetic field and higher torque.
- Stator field strength – Stronger permanent magnets or higher current in field coils increase torque.
- Armature current – Higher current produces greater torque as it strengthens the rotor magnetic field.
- Air gap between stator and rotor – A smaller air gap results in greater torque generation.
Starting and Running Torque
Brushed DC motors need high starting torque to overcome inertia and start rotating from rest. Once running, lower torque is required to sustain rotation at a nominal speed.
Series and compound motors provide very high starting torque but Permanent magnet and shunt motors have lower starting torque.
Speed Control of Brushed Motors
The speed of a brushed DC motor depends on the voltage applied and the load. Controlling speed is essential for most applications.
Methods of Speed Control
- Varying supply voltage using a variable DC power supply, rheostat or PWM control.
- Changing the strength of stator magnetic field in shunt/compound motors by controlling field current.
- Using a gearbox or pulley system to mechanically alter output speed.
- Electrical braking by shorting the motor terminals through a resistor when reducing speed.
Effects of Load
Speed decreases under increasing mechanical load as the motor needs more torque. Speed remains fairly constant from no load to full load in series and compound motors. But shunt motors lose speed significantly with load due to their low starting torque.
Efficiency of Brushed DC Motors
Efficiency indicates how much input electric power is converted to mechanical output power. Key factors affecting efficiency:
- Friction and windage losses – Can be minimized with proper design, bearings and enclosure.
- Stator and rotor core losses – Dependent on material properties and frequency.
- Copper losses in windings – Related to winding resistance and current.
- Brush contact losses – Account for around 2% loss.
Well-designed brushed DC motors can achieve 75-90% efficiency at their optimum operating point.
Major Applications of Brushed DC Motors
Small Fan Motors
Used extensively in computers, appliances, etc. Their high reliability and variable speed make them ideal for fan drives.
Power Tools
Drills, circular saws, jigsaws, grinders, and sanders utilize brushed motors up to a few horsepower. Compact size and torque are key factors.
Electric Vehicles
Brushed series wound DC motors provide high starting torque and variable speed control suited for electric bikes, golf carts, forklifts, etc.
Starter Motors
High starting torque allows series motors to crank and start internal combustion engines in cars, motorcycles, etc.
Robotics Actuators
Compact permanent magnet DC motors provide precise position, speed, and torque control as robot actuators.
Industrial Applications
Brushed DC motors drive machine tools, winding/textile machinery, conveyors, paper mills, pumps, presses, etc requiring adjustable speed.
So whether used in small appliances, automobiles, or factories around the world – brushed DC motors play an indispensable role in everyday activities and industrial processes.
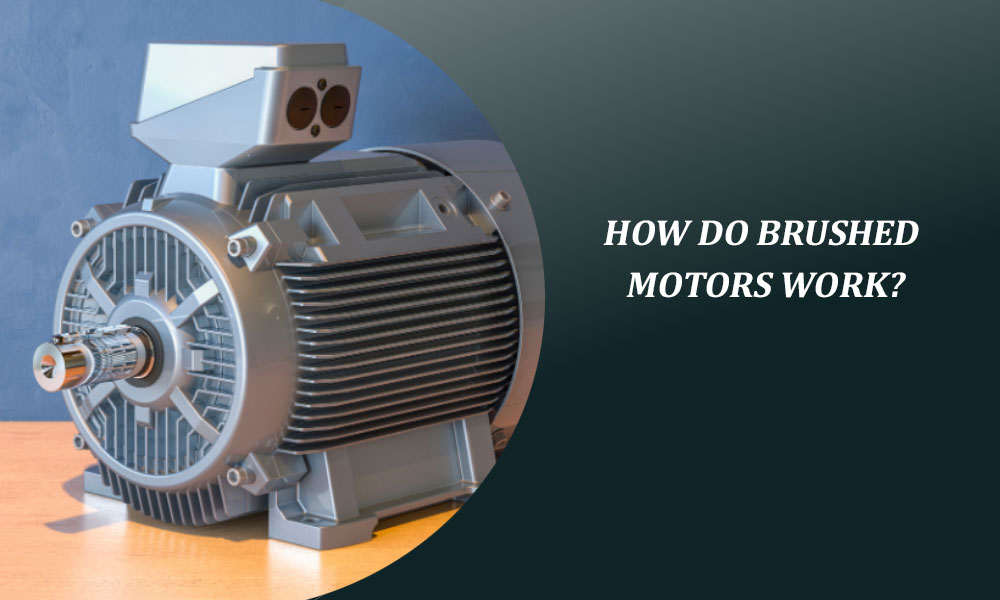
FAQs
What are the main components of a brushed DC motor?
The key components are the stator providing magnetic field, the rotor with windings, commutator and brushes to supply current, the axle, and the housing. Stator uses permanent magnets or wound field coils.
How does varying applied voltage control motor speed?
Higher voltage increases armature current, generating a stronger rotor magnetic field. This causes faster rotation under the fixed stator field. Lower voltages reduce speed.
What is the difference between shunt and series motors?
Series motors connect stator fields in series with armature providing high starting torque. Shunt fields are in parallel allowing easy speed control but with lower starting torque.
Why do the brushes and commutator wear out over time?
Frictional contact as brushes slide over the rotating commutator segments gradually erodes the brush and commutator material over prolonged use.
What maintenance is required for brushed motors?
Regular inspection of brushes, and replacement before they are fully worn out. Lubricating bearings, ensuring good ventilation, and cleaning out dirt and debris.
Conclusion
Brushed DC motors have been integral to industry and daily life for over a century now. From revolutionizing manufacturing with electric machinery to powering electric vehicles today, they continue going strong.
The simple yet ingenious electromechanical design converts electricity into rotary motion reliably and efficiently. Permanent magnet, shunt, series, and compound wound topologies allow tailoring brushed motors precisely to the required application.
Advances like neodymium magnets and electronic control have enhanced brushed motor performance and controllability. While brushless DC motors take over some applications, the cost-effectiveness, ease of use, and durability ensure brushed motors continue playing a major role.
So the next time you press the power button on a device, remember the trusty brushed motor silently spinning away! With regular maintenance, this workhorse technology will keep pace with modern demands for years to come.
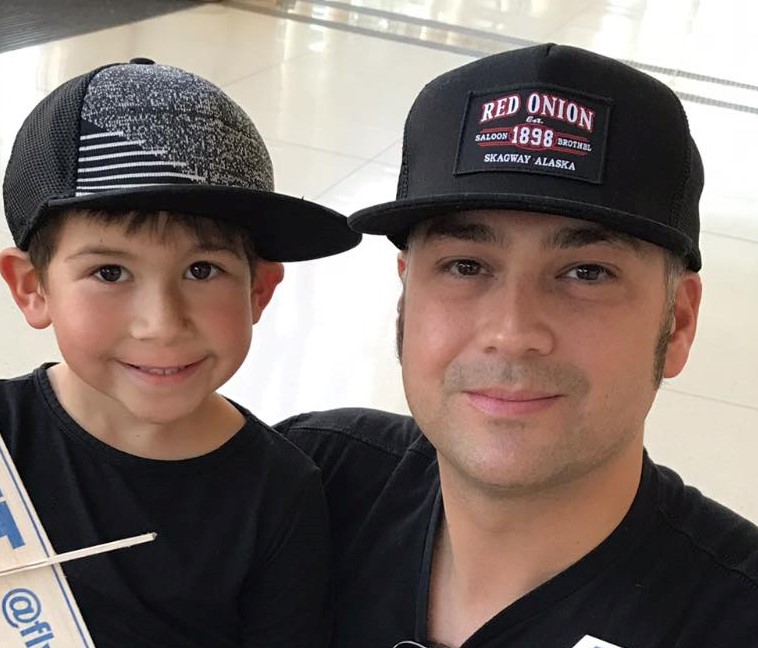
I am Jaxon Mike, the owner of the Rcfact website. Jaxon Mike is the father of only one child. My son Smith and me we are both RC lovers. In this blog, I will share tips on all things RC including our activities, and also share with you reviews of RC toys that I have used.