Last Updated on December 15, 2024 by Jaxon Mike
Electric motors are essential components of many devices and systems. From small hobby motors to industrial equipment, selecting the right motor type for an application is crucial. Two of the most common types of DC motors are brushed DC motors and brushless DC motors (BLDC). While both convert electrical energy into mechanical energy, they have distinct designs, characteristics, and pros and cons.
In this article, we will compare brushed vs brushless motors in depth. We will examine how each type works, their applications and uses, advantages and disadvantages, and factors to consider when choosing between them. Whether you are an engineer, hobbyist, or simply want to learn more about motor technology, this guide will provide a helpful overview of these two common motor types.
Here is an in-depth comparison table for the pros and cons of brushed vs brushless motors:
Brushed DC Motor | Brushless DC Motor | |
How it Works | Mechanical commutation using brushes and commutator | Electronic commutation synchronized to rotor position |
Construction | Wound armature rotates within permanent magnet stator | Permanent magnet rotor rotates within wound stator |
Cost | Lower cost simpler construction | More expensive due to electronics |
Efficiency | Typically 75-80% efficient | 80-90%+ efficient |
Maintenance | Brushes wear and require replacement | Minimal maintenance without brushes |
Noise | Brush sparking creates audible noise | Quiet operation with electronic commutation |
Speed Control | Easy to control speed by varying voltage | Requires electronic speed controller |
Low Speed Torque | Excellent torque at low speeds | Reduced low-speed torque capability |
High Speed Capability | Limited top speed due to mechanical commutator | High maximum speeds achievable |
Torque Delivery | Less smooth torque delivery | Very smooth torque curve |
Lifespan | Brush wear limits lifespan to hundreds of hours | Bearings are only wearing part, thousands of hours |
Reliability | Prone to dust/debris causing faults | Enclosed electronics improves reliability |
Electrical Noise | EMI from brush sparking | Minimal EMI noise |
Applications | Small appliances, power tools, toys, actuators | Computer fans, drones, RC vehicles, robotics |
BEST ONE | CHECK LATEST PRICE | CHECK LATEST PRICE |
How Brushed DC Motors Work
Brushed DC motors have been around for over a century and remain one of the simplest and most cost-effective motor designs. In a brushed DC motor, permanent magnets surround a coil of wire called an armature. Electric current from the brushes passes through the armature coils, generating electromagnetic fields that cause the armature to spin.
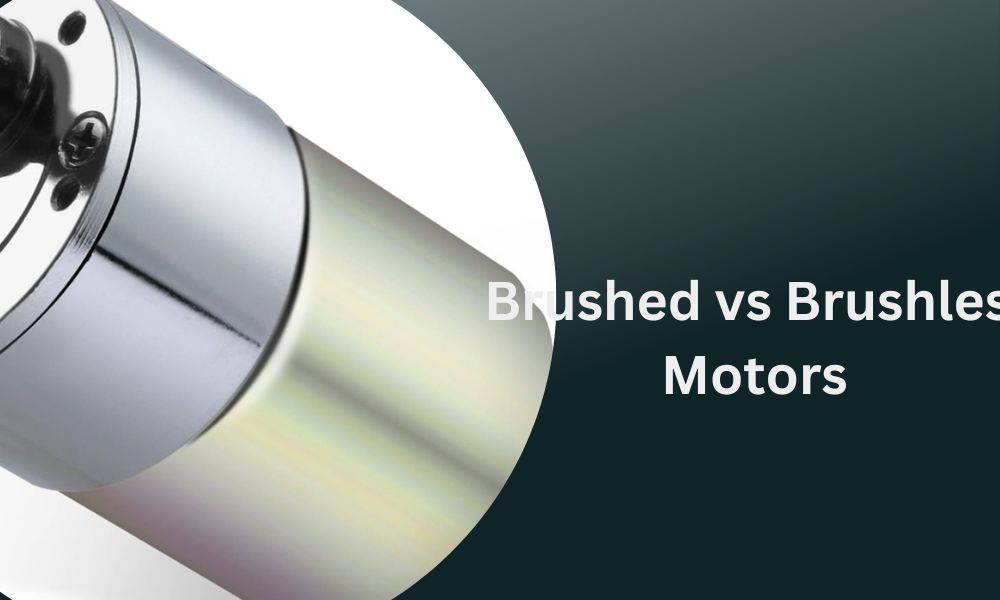
As the armature rotates, the coils come into contact with the permanent magnets in alternating north-south polarities, creating a continual torque. The armature contains a commutator, which is a cylinder divided into insulating copper segments. The brushes press against the commutator, transmitting electric current to the armature windings.
As the armature turns, the brushes slide onto different segments of the commutator, changing the direction of the current flow and allowing the armature to continue rotating smoothly. This commutation process gives brushed DC motors their characteristic high torque at low speeds.
Applications and Uses of Brushed Motors
Thanks to their simple design, low cost, and ability to provide high torque at low speeds, brushed DC motors have many applications:
- Small consumer appliances: Mixers, blenders, fans, power drills
- Toys and hobby products: Toy cars, model trains, quadcopters
- Industrial machines: Conveyors, pumps, servos, actuators
- Automotive: Window motors, windshield wipers, seat adjusters
In most applications, brushed DC motors are used with a drive circuit that regulates voltage and current to control motor speed and torque. They can achieve speed control across a wide range with good precision.
Pros of Brushed DC Motors
Low Cost: Brushed DC motors are inexpensive to manufacture compared to other motor types. The mechanical commutator and brushes are simple components that keep costs down.
Easy Speed Control: The speed of brushed motors can be easily varied by changing the voltage applied to the armature. Lower voltage results in slower speeds.
High Torque Capabilities: The brushes pressing on the commutator allow high current flow and strong electromagnetic fields for potent torque generation. This makes them well suited for applications requiring low speed, high torque operation.
Simple and Rugged Design: Brushed motors have an uncomplicated construction with few parts vulnerable to damage. This rugged design enables them to operate reliably with minimal maintenance.
Well-Understood Technology: Brushed motor technology is mature and well-documented. Their behavior and control methods are predictable for engineers and designers.
Cons of Brushed DC Motors
While brushed DC motors have benefits, they also come with distinct drawbacks:
Commutator Wear: The constant friction between the brushes and commutator causes wear over time. Brushes and the commutator must be replaced periodically.
Maintenance: Regular inspection of brushes and commutator bars is required. Brushes may need cleaning or replacement to prevent damage from debris buildup.
Sparking: As the brushes move between commutator segments, electrical arcing can occur. This sparking limits use in explosive environments.
Electrical Noise: Sparking in the commutator generates electromagnetic interference (EMI). Shielding is required for electronics-sensitive uses.
Lower Efficiency: Brushed designs have more components causing energy losses like friction and resistance heating. Efficiency is generally 75-80% at full loads.
How Brushless DC Motors Work
Brushless DC motors (BLDC) take a different approach to electromechanical energy conversion. Instead of brushes and a commutator, BLDC motors rely on permanent magnets and electronic control for commutation.
In a brushless DC motor, the permanent magnets are part of the rotor assembly which rotates, while the armature coils remain static as part of the stator. The rotor contains permanent magnet pole pairs which create a magnetic field that penetrates the stator.
The stator contains several windings of wire coils. As current runs through each coil, it generates a localized magnetic field. The electronic drive circuitry energizes the coils in sequence, causing the rotor to turn in response to the alternating magnetic forces.
Hall effect sensors detect the rotor’s position and feed that information to the motor controller. This allows the controller to properly time the commutation and energize the windings in sync with the rotor movement.
With electronic commutation instead of a mechanical commutator, brushless motors avoid issues like sparking and wear. The rotor and bearings are the only moving parts in a brushless design.
Applications and Uses of Brushless Motors
Some common applications taking advantage of the benefits of brushless DC motors include:
- Computer peripherals – Hard drives, optical drives, printers
- Electric bicycles and scooters
- Drones and quadcopters
- Robotics – Servos, linear actuators
- Automotive – Power windows, adjustable pedals and seats
- HVAC equipment – Fans, pumps
- Appliances – Vacuums, blenders, washers
Brushless motors excel in applications requiring smooth operation, precision speed variability, high speeds, frequent on/off cycling, or operation in dirty/harsh environments. Their electronic commutation makes them well suited for positional or servo control tasks.
Pros of Brushless DC Motors
Higher Efficiency: Absence of brushes and commutator minimizes energy losses. BLDC efficiencies range from 80-90% or more.
Low Maintenance: No contact brushes or commutator bars to wear down over time. Bearings just need occasional lubrication.
Long Lifespan: Brushless motors last substantially longer than brushed equivalents, with lifespans of 20,000 hours or more.
Noise Reduction: Lack of sparking and quieter operation due to precise electronic commutation instead of mechanical.
High Torque and Speed Range: Strong neodymium magnets and advanced controls allow excellent torque output and speed control.
Better Speed vs. Torque Curve: Brushless motors can provide higher torque at low speeds than brushed types.
Minimal Electrical Noise: With electronic commutation instead of sparking brushes, EMI noise is greatly reduced.
Cons of Brushless DC Motors
Despite the advantages, brushless motors also have some downsides:
Higher Cost: The construction is more complex than brushed motors, with permanent magnets and electronic control requirements. This equates to higher costs.
Advanced Controls Needed: Brushless motors cannot operate directly off DC power. They require speed controllers to orchestrate commutation.
Permanent Magnets: Neodymium magnets can be expensive and vulnerable to demagnetization from heat or external magnetic fields.
Limited Very Low Speed Control: At extremely low speeds, brushless motors lose torque compared to brushed designs.
Torque Ripples: The timing of energizing coils can cause subtle torque pulsations, an issue for applications requiring ultra-smooth operation.
More Electronics: In addition to the motor itself, brushless systems require rotor position sensors and programmable control electronics.
Direct Drive vs Geared Brushed and Brushless Motors
Motors are often described as either direct drive or geared. This refers to whether the motor is directly coupled to the load or connected via a gear reduction system. Both brushed and brushless motors can be found in either direct drive or geared configurations.
Direct drive motors directly couple the rotor shaft to the driven load. This provides excellent low-speed control and torque. Speed and torque will change together in a fixed ratio. Direct drive enables accurate speed regulation without any play or backlash from gears.
Applications include conveyors, sliding doors, robot joints, and precision position control systems.
In contrast, geared motors use a gearbox to either increase or decrease the motor’s torque and speed. Common gear types include spur gears, planetary gears, and worm drives. Compared to direct drive, geared motors offer:
- Ability to optimize motor speed while independently controlling load torque and speed.
- Operation at speeds or torque levels not achievable directly from the motor.
- Changing load conditions will not directly impact motor operation.
Geared motors are more complex and lower in efficiency but excel when an application requires different speed or torque than the motor can provide directly. Geared versions of both brushed and brushless motors are widely available.
Choosing Between Brushed and Brushless Motors
With an understanding of the pros and cons of brushed vs brushless DC motors, here are some key factors to consider when selecting the best type for an application:
Cost Constraints: If budget is a major concern, brushed motors offer significant cost savings, especially for low-duty cycle applications.
Efficiency Requirements: Brushless designs far surpass brushed motors in terms of energy efficiency. Important for battery powered mobility applications.
Maintenance Factors: Brushless motors minimize maintenance needs. Useful where motor access is difficult or downtime is detrimental.
Noise: Brushed motor arcing creates noticeable noise. Brushless operation is quieter for applications where noise is problematic.
Control Interface: Brushed motors can operate directly from DC voltage. Brushless motors require electronic speed controllers.
Speed and Torque: Brushless enables a wider speed range and torque curve, while brushed excels at lower speeds.
Lifespan: Brushless motors last many times longer than brushed equivalents. Helps when replacement is difficult.
Environment: Harsh or dirty operating environments favor a brushless design with enclosed electronics.
Considering these factors will help guide the selection process when choosing between brushed or brushless motors.
Frequently Asked Questions
What is the difference between a brushed and brushless motor?
Brushed motors use mechanical commutation with brushes and a commutator. Brushless motors use electronic commutation synchronized to the rotor position with no physical contact brushes.
Do brushless motors have more torque?
Yes, brushless designs can achieve higher torque across much of the speed range compared to brushed equivalents. Strong neodymium magnets contribute to increased torque capabilities.
Are brushless motors better?
Brushless motors have advantages in many applications thanks to increased efficiency, reliability, precision speed control, noise, and lifespan. But brushed motors still excel in simplicity and low-speed torque situations.
Do brushless motors wear out?
Brushless motors have no brushes to wear out and replace. Their lifespans are dramatically longer than brushed motors, often over 10 times as long before failure.
How long do brushless motors last?
Properly maintained and operated within ratings, a brushless motor may last 20,000 hours or more. That equates to 10+ years of continuous operation. Lack of friction and arcing commutation greatly extends lifespan.
Conclusion
While brushed and brushless motors employ very different designs, both can be useful for a range of applications. Brushed motors offer simplicity, low cost, and excellent control at low speeds. Brushless motors trade that simplicity for increased efficiency, reliability, lifespan, and performance across a wider operating range.
Here are some final recommendations on selecting between motor types:
- For power tools, small fans, servos or other short duty-cycle devices, brushed DC motors are a great low-cost choice.
- Lifespan and maintenance are priorities, brushless motors are favored, despite their higher initial cost.
- Applications needing efficiency and precision speed control will benefit substantially from brushless capabilities.
- Very low speed, high torque demands like traction may still be better served by brushed motors.
- Consider gearheads or gearboxes if the inherent speed/torque curve of either motor type is unsuitable.
Hopefully this guide has provided a helpful overview of the pros and cons of brushed vs brushless motors. Understanding their distinct advantages allows selecting the best motor technology for any electromechanical power application.
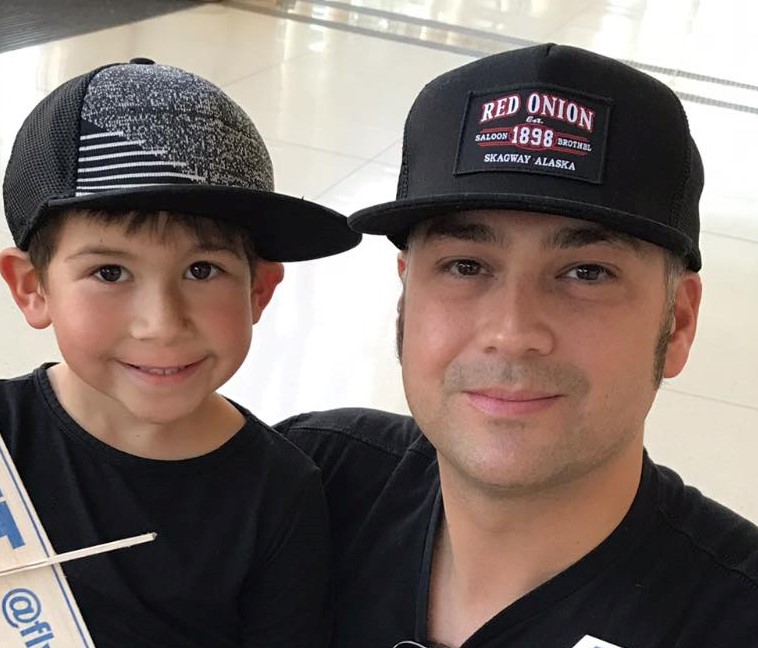
I am Jaxon Mike, the owner of the Rcfact website. Jaxon Mike is the father of only one child. My son Smith and me we are both RC lovers. In this blog, I will share tips on all things RC including our activities, and also share with you reviews of RC toys that I have used.