Last Updated on July 14, 2025 by Jaxon Mike
Servos are electromechanical devices used widely in robotics and automation applications. They allow precise control of angular position, velocity and acceleration.
There are two main types of servos – analog and digital. While both operate on the same basic principle, there are some key differences between the two that impact their performance and applications.
This article provides a comparative analysis of analog and digital servos. We will examine how each type works, their components, advantages and disadvantages, use cases and help you determine which one works best for your needs.
Digital vs Analog Servo: A Complete Comparison
Parameter | Analog Servo | Digital Servo |
Control Circuitry | Analog transistors and op-amps | Microcontroller and digital electronics |
Position Sensing | Potentiometer | Optical/magnetic encoder |
Accuracy | Low (5-10 degrees) | Very high (0.1 degrees or better) |
Resolution | Low (~5 degrees) | High (as low as 0.005 degrees) |
Speed | 50-600 rpm | Up to 7200 rpm |
Latency | High (~200 ms) | Low (20-30 ms) |
Torque Capacity | Very high | Moderate-High |
Power Consumption | Low | Moderate |
Durability | Medium | High |
Noise | Medium | Low |
Cost | CHECK LATEST PRICE | CHECK LATEST PRICE |
How Servos Work
A servo has three key components:
- Motor: Provides the mechanical power to drive the output shaft
- Control circuitry: Applies power to the motor and controls its position
- Position sensor: Provides feedback on the current shaft position
The basic working principle of a servo is simple:
- The control circuitry receives a command for a specific angular position.
- It powers the motor to move the output shaft.
- The position sensor continuously feeds back the real-time position.
- This feedback loop allows the control circuitry to stop the motor precisely at the commanded position.
The main difference between analog and digital servos lies in the control circuitry and position sensor. Let’s look at both types in more detail.
Analog Servos
Analog servos have been around since the 1960s. They use analog circuitry for control and a potentiometer for position sensing.
Components:
- Motor: Small DC motor with gearing to provide high torque
- Potentiometer: Measures position of output shaft and provides analog feedback voltage
- Control circuitry: Uses analog components like transistors and operational amplifiers
Working:
- The input is a PWM (pulse width modulated) signal that represents the desired angle.
- This is compared with the potentiometer’s position voltage.
- The circuit amplifies the difference to drive the motor and reduce the error.
- This continues till the pot voltage equals the input PWM pulse width.
Pros:
- Inexpensive
- Simple and easy to repair
- High torque capacity
Cons:
- Low resolution and accuracy
- Higher latency due to analog feedback loop
- Prone to noise interference
Digital Servos
Digital servos utilize digital electronics for control and sensing. They offer better precision and faster response than analog variants.
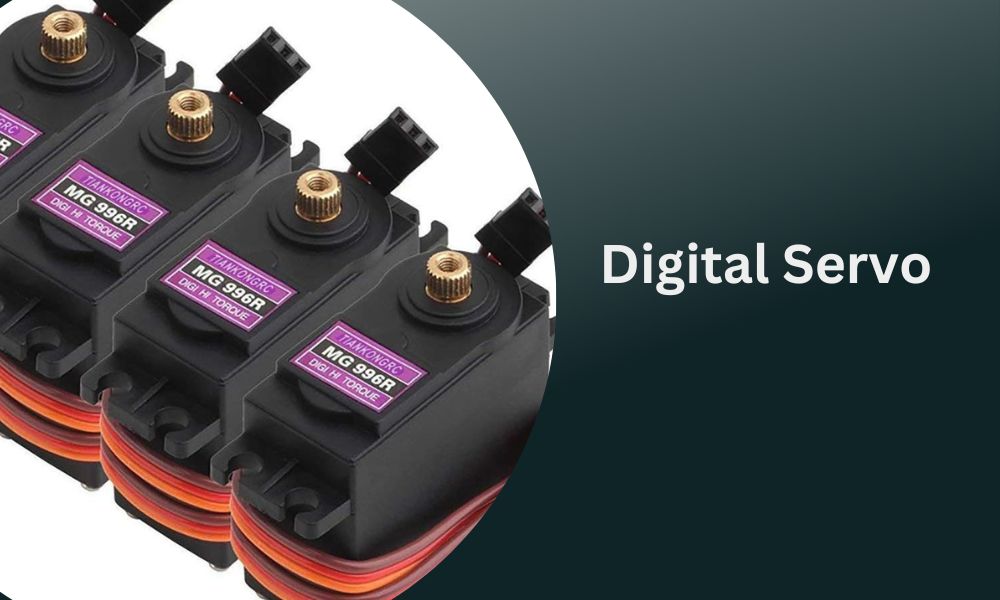
Components:
- Motor: Similar to analog servos but may be smaller since less torque is required
- Encoder: High resolution digital encoder for sensing shaft position
- Control circuitry: Uses a microcontroller and digital components
Working:
- Input is a digital PWM signal representing desired position
- This is compared with encoder position by the microcontroller
- Error is calculated and the drive signal to motor adjusted accordingly
- Much faster sensing and control loop updates due to digital implementation
Pros:
- Higher accuracy and resolution
- Faster speed and lower latency
- Immune to noise interference
- Features like overload protection can be easily added
Cons:
- More expensive than analog
- Controller programming required
- Not easily repairable
Key Differences
Now that we have seen how analog and digital servos work, let’s highlight some of the key differences between them:
Accuracy and Resolution
The position sensing mechanism is the main factor impacting accuracy. Potentiometers have low resolution while encoders provide precision down to fractions of a degree. This allows digital servos to achieve sub-degree accuracy.
Speed and Latency
Digital servos have faster control loops so they can react quicker with lower latency. Some high-end digital servos can reach speeds up to 0.03 seconds/60 degrees.
Torque and Power Consumption
Analog servos can provide very high torque capacity since power requirements are lower. Digital servos with smaller motors may have lower torque but make up for it with advanced control algorithms.
Durability and Noise
Potentiometers in analog servos are mechanically rotated which affects lifetime. No such issues exist in digital encoders, providing longer service life. Digital servos also operate much more quietly.
Cost
Analog servos are priced from $5 to $20 while digital variants start from $30 and go up to hundreds of dollars. The sophisticated electronics require higher investments.
Use Cases and Applications
Analog Servos
Due to low cost and adequate performance, analog servos are ideal for:
- Simple hobbyist robot projects
- Basic automation systems
- Applications not requiring high precision
Digital Servos
Digital servos are preferred for:
- Industrial robots, CNC machines
- High performance RC vehicles and drones
- Aerospace/defense applications
- Medical devices and prosthetics
For most consumer robotics projects, analog servos are sufficient. But for commercial systems requiring precision and reliability, digital is the way to go.
FAQs
How are analog servos controlled?
Analog servos are controlled by sending a PWM (pulse width modulated) signal that represents the desired angular position. Standard hobbyist servos use a PWM range of 1-2 ms within a repeating 20ms period.
What is the maximum operating speed of analog servos?
Most standard analog servos can operate at maximum speeds of 50-60 degrees in 0.10 – 0.16 seconds which gives around 300 to 600 rpm. Specialized high-speed analog servos are capable of speeds up to 0.03 secs/60 degrees.
What is the resolution of digital servos?
Digital servos using high resolution absolute encoders can achieve a resolution between 0.1 and 0.9 degrees. Very high precision models boast resolutions of 0.005 degrees or even higher.
How do digital servos achieve overload protection?
Overload protection is implemented in the servo controller software by monitoring the motor current. If the current exceeds a predefined threshold, power to the motor is cut off to prevent damage.
Which type of servo is better for high torque applications?
Analog servos can provide exceptionally high torque capacity – up to 300 kg/cm or more. Their mechanical gearing and simplicity allows them to produce very high torque despite lower power motors.
Conclusion
Analog and digital servos each have their own strengths and applications. Analog types are inexpensive, easy to find and repair, provide high torque capacity and decent performance for basic projects.
For tasks needing high accuracy, quick response times and reliability like industrial automation and advanced drones, digital servos are the better choice despite higher costs.
Consider resolution, speed, torque needs and operating environments when deciding between the two. For highly demanding performance requirements, choose digital, otherwise analog servos may suffice if precision is not critical.
This covers the key differences between these two servo technologies. The next part of the article will provide more details on use cases, selection criteria and recommendations when choosing between analog and digital servos.
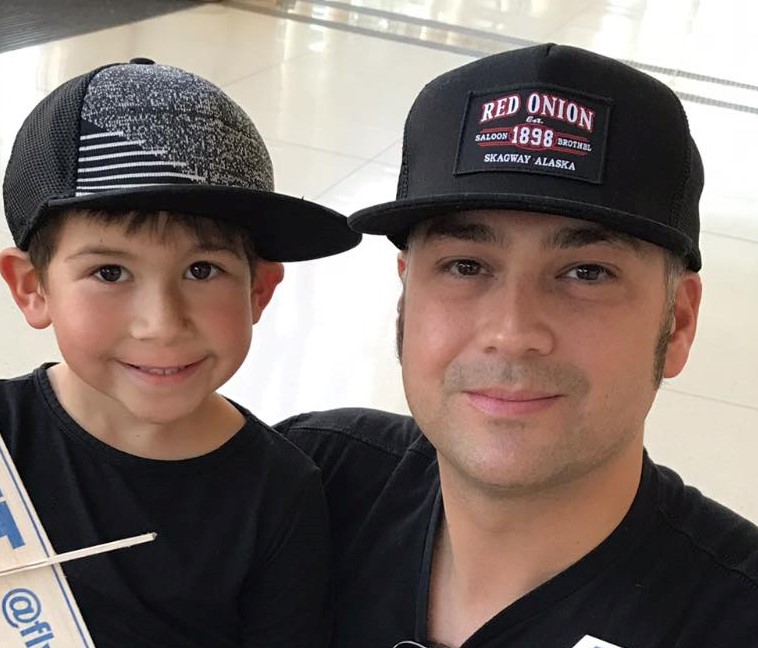
I am Jaxon Mike, the owner of the Rcfact website. Jaxon Mike is the father of only one child. My son Smith and me we are both RC lovers. In this blog, I will share tips on all things RC including our activities, and also share with you reviews of RC toys that I have used.